Quality Control
For product materials and quality, we strictly adhere to MXG inspection procedures and standards, as well as relevant ISO standards. This includes material inspection reports, First Article Inspection (FAI), Coordinate Measuring Machine (CMM) final inspection reports, and industry-specific reports such as PPAP and FMEA as required by our clients. Our ultimate goal is to ensure our products are 100% safe to use.
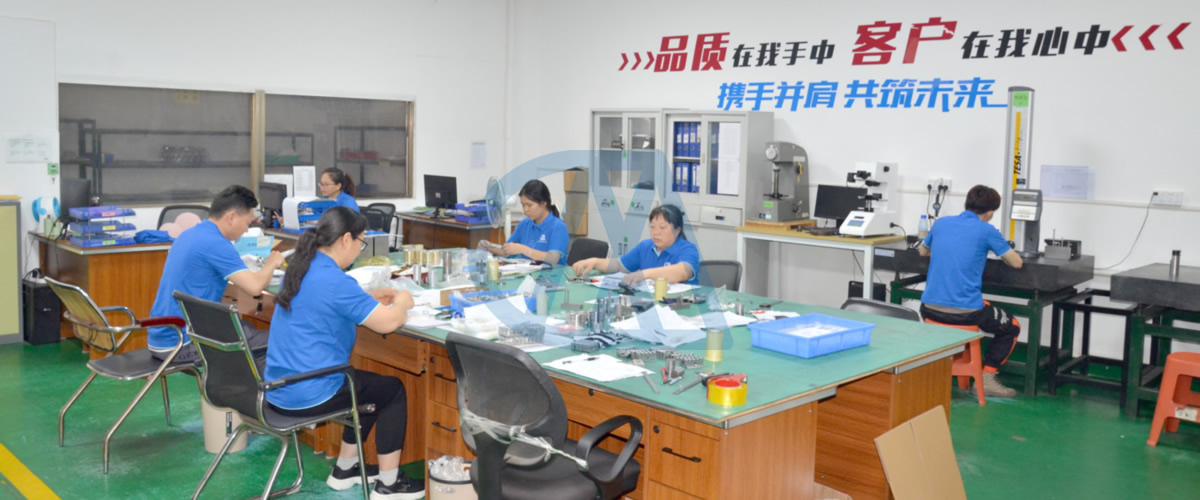
Quality Inspection and Testing
● IQC
All incoming materials must be inspected by spectrum detector to ensure the authenticity.
● In-Processing-Inspection
Each product needs to go through a first article inspection (FAI) and be verified by engineering or quality managers.
● Inventory check
Before warehousing, 100% of the products must be inspected
● Pre-shipment inspection
Check again and record the delivery report before shipment
● Check on Testing Equipment
Regularly calibrate and record the date
● Our Test Tools and Equipment
Calipers
Inside/Outside diameter micrometer
Pin gauge/Gauge block / Plug gauge
Thread/plug gauge (Metric/inch)
2D&3D CMM
Material spectrometer
Hardness tester
Laser Lettering and Paper Labelling
Our Quality Documents
Material Composition Test Report
● Inspection of Product Appearance and Packaging
After completing the surface treatment of parts, it is essential to verify that the dimensions and appearance meet the specified requirements. Customized packaging is used to ensure that the product remains undamaged during delivery.
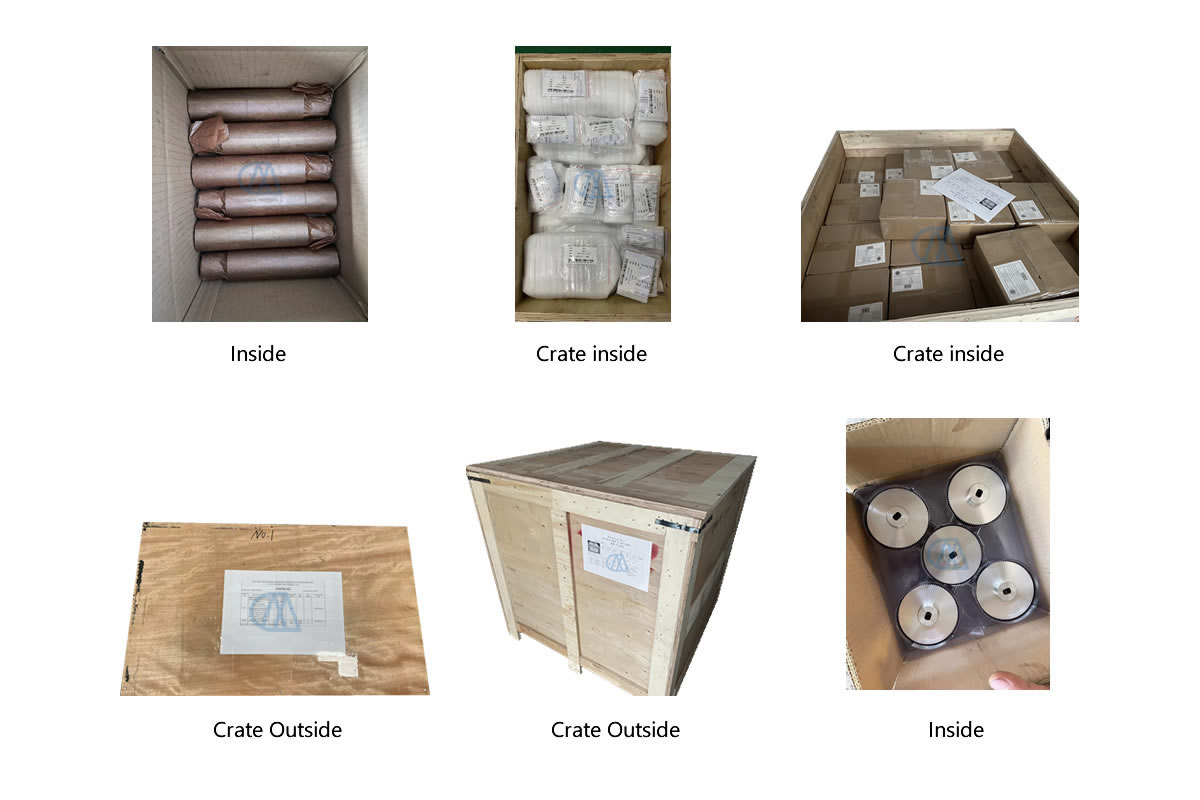
● ISO Certification
Improving customer satisfaction is our first priority, meanwhile, we fully compliant with the latest ISO requirements to evaluate and prevent any possible risks before production, which enable us to offer our customers with defect free products and services. Besides, regularly follow-up visit, telephone, survey are our tradition to continuously improve and upgrade our team.
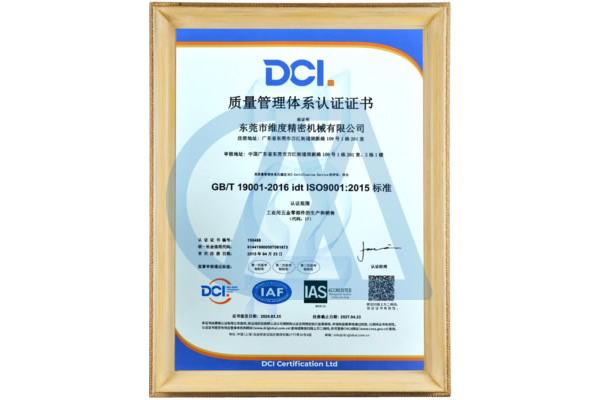
Quality Problem Solution
At MXG, we are committed to delivering exceptional custom mechanical parts tailored to your specific needs. Should our products or services fall short of your expectations, we offer rework or refund options. If you experience any quality issues within one month of receiving your order, please contact your sales representative. We will respond promptly and provide a suitable resolution upon receipt of your notification.
Rework Conditions
If you encounter a quality issue, please contact us immediately. We will convene a meeting to re-examine the design and samples. If the issue is rectifiable, we will arrange for the return and repair of the parts. Concurrently, we will dispatch replacement parts to you. Common re-workable issues include:
1. Finishing defects,
2. Tolerance discrepancies,
3. Heat treatment problems.
Refund Conditions
Upon receiving email feedback, we will promptly initiate video or telephone communication to verify that the product issue is attributable to us and is irreparable. If confirmed, we will expedite the process of refunds and returns. Common reasons for refunds include:
1. Incorrect material,
2. Tolerance discrepancies,
3. Quantity shortages,
4. Other defects.